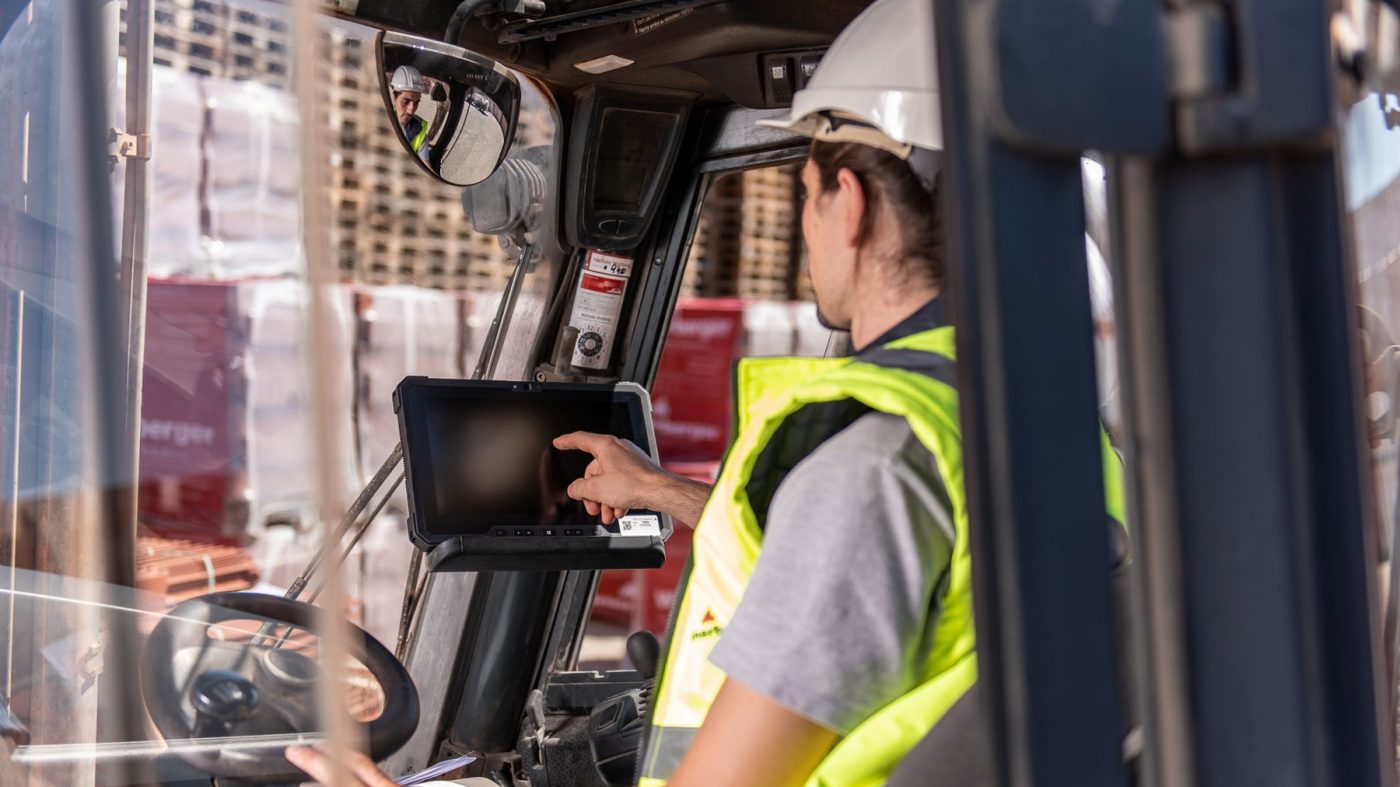
Digital Stockyard: Information in Real-Time
Wienerberger gets storage logistics fit for the future with the Digital Stockyard solution: All data is collected and forwarded electronically and in real-time.
Wienerberger gets storage logistics fit for the future with the Digital Stockyard solution: All data is collected and forwarded electronically and in real-time.
What processes and intermediate steps does stockyard management involve? Where does an inbound truck driver check in with his vehicle? And how does a forklift operator know that a load is ready for pick up? These and similar questions formed the starting point for Wienerberger’s digital stockyard project to digitize stockyard logistics and make them even more efficient.
From picking the products to issuing dispatch notes to truck drivers: in the past, many of the steps required for the acceptance, storage and loading of merchandise had to be repeated and performed manually. The Digital Stockyard solution introduced in 2019 simplifies these processes and ensures that information is collected and forwarded in real-time.
“This project has made the paperless stockyard reality. No other company has a completely digital end-to-end-solution like the one we have developed”, says Günther Gfrerrer, Head of Supply Chain Management at Wienerberger. After having first gone live in the Netherlands and Belgium, the Digital Stockyard solution has now been implemented in several of Wienerberger’s other international markets, including Austria.
The process is as follows: The “picker“ assembles the individual items for the consignment based on the customer’s order. This is then followed by the digital check-in for the truck driver. After checking in via a touchscreen, the driver is shown all the information he needs to proceed – from the safety measures in force at the site to the merchandise and the allocated loading bay. The forklift operator in the stockyard is notified in real time that check-in has taken place. He can view all the data regarding orders and drivers on a tablet and process it in the SAP-system using a special user interface. Photographs to document the loading of the consignment can also be attached.
The merchandise is now loaded onto the truck. Once the truck has been fully loaded it is time to continue to the digital check-out. If the load does not match the dispatch note, it is automatically corrected. The truck driver confirms that he has accepted the goods by signing for them. The advantage of this procedure is that it provides a real-time inventory that always reflects actual stock levels. Moreover, no further administrative steps are required.
Digital stockyard management enables completely paperless processing, thus reducing administrative tasks. Workflows are faster and simpler as unnecessary duplication is eliminated. “Inventory data that is updated in real time and the precise sequencing of delivery trucks reduce waiting times. The system also prevents errors when the vehicles are loaded”, Gfrerrer explains.
The Digital Stockyard solution facilitates storage planning and enables greater flexibility. In the event of changes during the loading process, the dispatch note is automatically corrected. A particular advantage during the corona pandemic is that the entire process can now be made contactless.
Inventory data that is updated in real time and the precise sequencing of delivery trucks reduce waiting times. The system also prevents errors when the vehicles are loaded.
“Our forklift operators had already been calling for digitization. Now they can work with a modern device which also makes the job more appealing”, says Günther Gfrerrer. Forklift operators are given tablets with large control buttons that are faster and easier to use. The system also uses color coding: “Green”, for example, stands for “standard process”. In winter, forklift operators are given special touchscreen gloves so they can stay connected in even the lowest temperatures.
The system knows exactly who has checked in and which external truck drivers are on site. If the safety requirements are not observed, loading can be stopped at any time. If a forklift operator finds a defect in his vehicle, he can report it to his supervisor immediately. Moreover, he no longer has to get out of the forklift to perform every task - so Digital Stockyard dramatically increases safety on site. It is hardly surprising therefore that feedback from the forklift drivers is positive.
When the solution was implemented, care was taken to ensure that it could be easily adapted to local needs. The Digital Stockyard app is currently available in 23 languages and the end devices are connected to the SAP system via the mobile network. The solution has already been implemented in 35 plants and is being rolled out to additional sites and markets on an ongoing basis. Wienerberger is already working on further solutions for storage logistics 4.0 - such as the link with the transport management system.