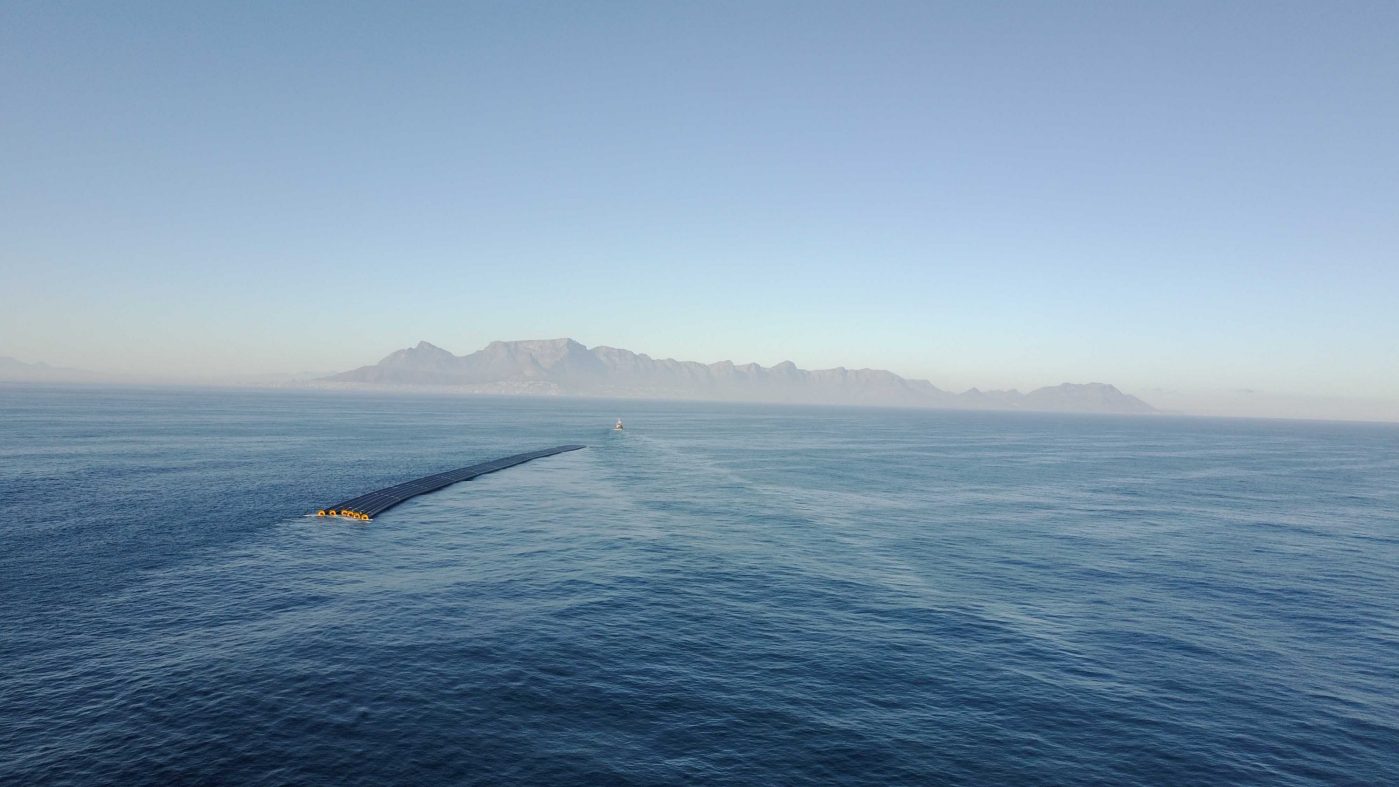
Recycling at Pipelife: A New Life for Plastic Pipes
This is how wienerberger’s subsidiary Pipelife advances plastics recycling: Opportunities and challenges on the way toward the circular economy.
This is how wienerberger’s subsidiary Pipelife advances plastics recycling: Opportunities and challenges on the way toward the circular economy.
With a service life extending over generations, plastic pipe systems ensure the safe transport of water, electricity or gas. To preserve the valuable raw material after its primary use, Pipelife has set itself ambitious recycling targets. wienerberger’s subsidiary thus supports the EU Plastics Strategy and contributes toward the advancement of the circular economy.
Every year, Pipelife processes hundreds of thousands of tons of plastics, mainly polyethylene (PE), polypropylene (PP) and polyvinylchloride (PVC). Many of the pipes made from these materials last for 100 years and more. Prolonging the useful life of the material is one of the goals of wienerberger’s Sustainability Strategy 2020+ in the environment sphere, alongside the protection of biodiversity and decarbonization.
We want to make our products 100% recyclable.
The targets set for the future are twofold: “On the one hand, we want to make our products 100% recyclable. In the future, we will be able to remove a pipe from its trench, recycle it and use it as secondary material for the production of a new pipe”, says Zoran Davidovski, Head of R&D and Sustainability at Pipelife. On the other hand, the re-use of materials of value must be ensured. “By giving plastics a second or third life, we keep them from ending up in the landscape and in the oceans.”
The growing amount of secondary raw materials used – up from 67 kilograms per ton of products in 2017 to 85 kilograms in 2019 – confirms the success of Pipelife’s efforts. In other words: Of 740,000 kilometers of pipes sold last year, 62,000 kilometers consisted of recycled plastics. This corresponds to a distance of 1.6 times around the world.
And there is more to come: A new cable conduit is made entirely of secondary raw materials. Other projects are being developed, such as the production of multi-layer plastic pipes in Germany and the Czech Republic. These pipes have thin outer and inner layers of virgin material and a middle layer of recycled plastics, the ratio of secondary raw materials to new materials being 80% to 20%.
“One of the biggest challenges is to find the type and quality of plastic material best suited for the product in question”, says Theodora Rompoti. As Head of International Plastics Raw Materials Purchasing, she is responsible for the procurement of raw materials for all Pipelife companies. Most of the secondary raw materials are derived from other products, such as plastic bottles and other waste. They are purchased in the form of pellets or powders and processed into new products.
One of the biggest challenges is to find the type and quality of plastic material best suited for the product in question.
Legal standards are another obstacle, especially in Europe. Currently, the use of secondary raw materials is still restricted in most applications due to standards from the past. “Together with TEPPFA, The European Plastic Pipe and Fittings Association, Pipelife has made considerable progress in working on the further development of the standards. However, a lot remains to be done”, emphasizes Davidovski.
Pipelife Netherlands developed a pipe with three lives: The plastic pipe can be re-used up to three times, which prolongs its service life to more than 300 years. You can tell the age of the pipe by its color: What begins life as a yellow low-pressure gas pipe, can be converted into a red cable conduit and is finally recycled into a grey sewer pipe. In this project, Pipelife cooperates with a Dutch gas network operator. The project received a prize at the 2019 INOVYN Awards.
Mechanical recycling meets its limits due to the composition of certain plastic materials or on account of legal requirements. New technologies will therefore have to be used in the future. Plastics made of several different raw materials can be recycled by a chemical process in which they are broken down into ethyl molecules. This technology is still in its infancy. At the same time, Pipelife is doing research on non-fossil, bio-based raw materials.
In the course of 2020, the amount of secondary raw materials in Pipelife pipes is to be increased to 90 kilograms per ton of products. To this end, the mechanical recycling of valuable substances is to be further improved. From the company’s perspective, chemical recycling also offers opportunities for the future. At the same time, the percentage of internal secondary raw materials is being increased. Considerable potential is also seen in the sorting of materials and the recycling process: Possibilities of doing it all within the wienerberger Group are being explored.
Innovation is a key to the circular economy. Demand for products made from recycling materials is increasing, but customers expect them to have the same properties and the same service life as products made from new materials. Extensive tests are therefore performed to evaluate the long-term performance of such products. Pipes are tested for crack resistance in the laboratory and under conditions of practical application.
We have seen enormous progress in the production of plastic materials. With so many things happening in this sector, we look to the future with optimism.
At the same time, Pipelife is working intensively on optimizing the design of its pipes and further improving their properties. “We have seen enormous progress in the production of plastic materials. With so many things happening in this sector, we look to the future with optimism”, says Zoran Davidovski.