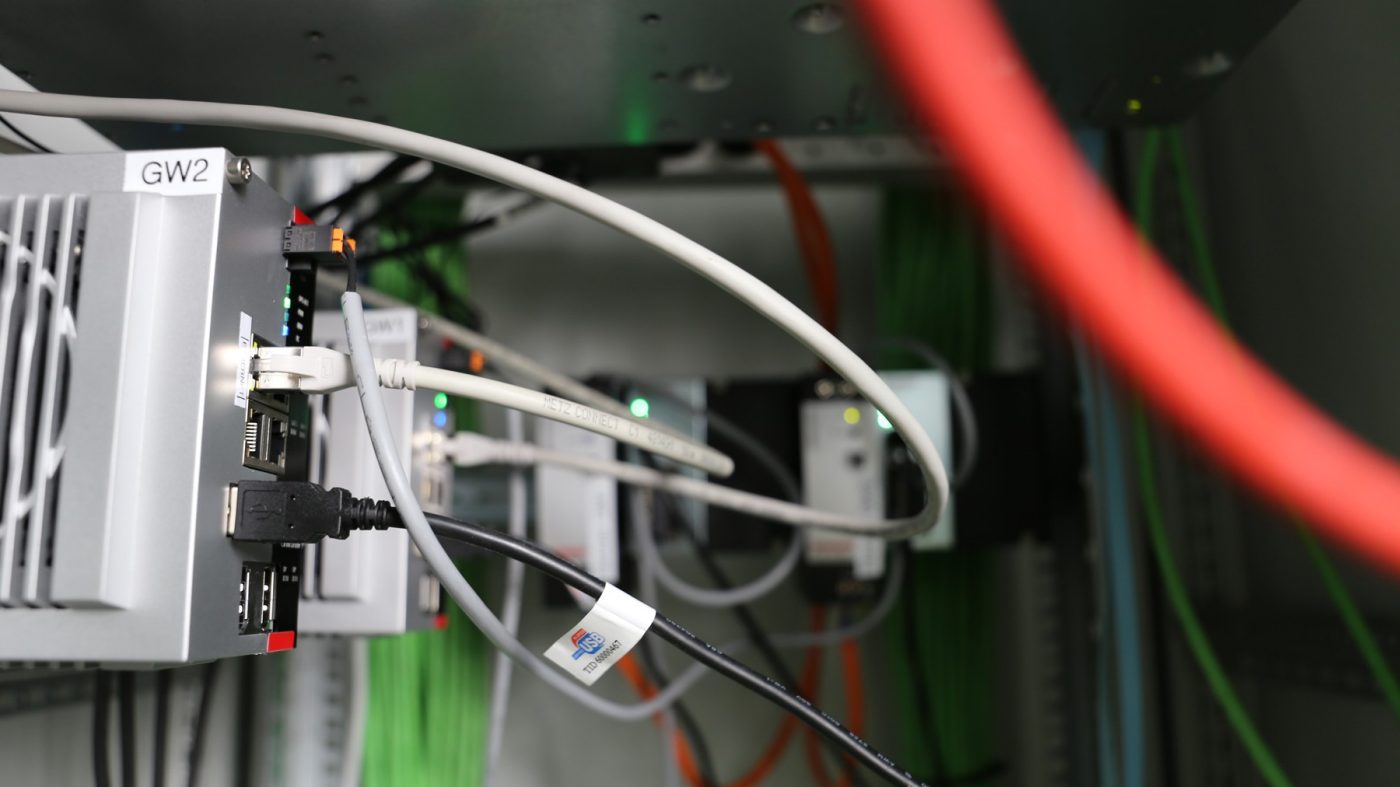
Data Management: Turbo-Charging Production
Transparent and user-friendly: Wienerberger is using professional data management to optimize production of bricks and piping systems.
Data Management: Turbo-Charging Production
Transparent and user-friendly: Wienerberger is using professional data management to optimize production of bricks and piping systems.
When a company has more than 200 production sites and over 3,200 production lines it isn’t always easy to keep track of things. But with the help of IT specialists from TietoEVRY, Wienerberger has taken data management for its Piping Solutions and Building Solutions Business Units to new levels. The project was nominated for the Austrian eAward 2021 in the Services and Process category. The award is organized by the special interest magazine Telekom Report.
In our digitalized world, data is a critical success factor: Companies use data to make informed decisions, add value to manufacturing and streamline their business processes. Due to its many production lines, Wienerberger has a wide range of machines and process control systems all of which provide valuable production data. This is where the current project comes into play. The goal was to use this information to optimize production processes by centrally collating local data and making it available to users throughout the Group. To do this, an economical, industrial-strength and scalable solution was developed.
“With our wide-ranging approach to digitalization, we helped Wienerberger record, store, analyze and visualize data streams.”
“With our wide-ranging approach to digitalization, we helped Wienerberger record, store, analyze and visualize data streams,” says Manuel Hausjell, IoT Consultant and Project Manager at TietoEVRY. A digital twin, that is a virtual mirror of the physical production facilities, was also created to enable real-time “end-to-end” data flows across a large number of processes and applications. This new solution for managing production data has allowed Wienerberger to achieve its ambition of having “All relevant data online – all the time.” This creates a solid foundation for a comprehensive utilization of data (keywords: artificial intelligence and machine learning).
Thousands of signals per second are transmitted to a central data hub in a cloud environment based on Microsoft Azure. This creates Group-wide transparency about the production sites and the performance of their machinery. All relevant employees – from engineers to plant managers – are then given user-specific access to applicable information. This enables them to learn from experience, improve day-to-day operations and enhance process efficiency.
“This is a massive step forward in our industry 4.0 plans. Thanks to this scalable solution we have achieved an unprecedented level of online transparency for our production lines.”
The new solution also ensures the scalability of production data for all production facilities and future requirements and enables cross-functional teams to gain valuable insights concerning raw materials, maintenance, machine settings and quality control for even more effective processes. “This is a massive step forward in our industry 4.0 plans. Thanks to this scalable solution we have achieved an unprecedented level of online transparency for our production lines,” says Roy Sibbald, Manufacturing Excellence Officer at the Wienerberger subsidiary Pipelife. Furthermore, production data is combined with order data and production planning data so that reports (based on Microsoft technology - PowerBI) can be used, for example, to facilitate a transparent and efficient shift handover in the plants.
The use of innovative solutions is part of Wienerberger’s strategy. Modern data management and the visualization of information has created a solid foundation for further digitalization projects.
Click to learn more
Click to close