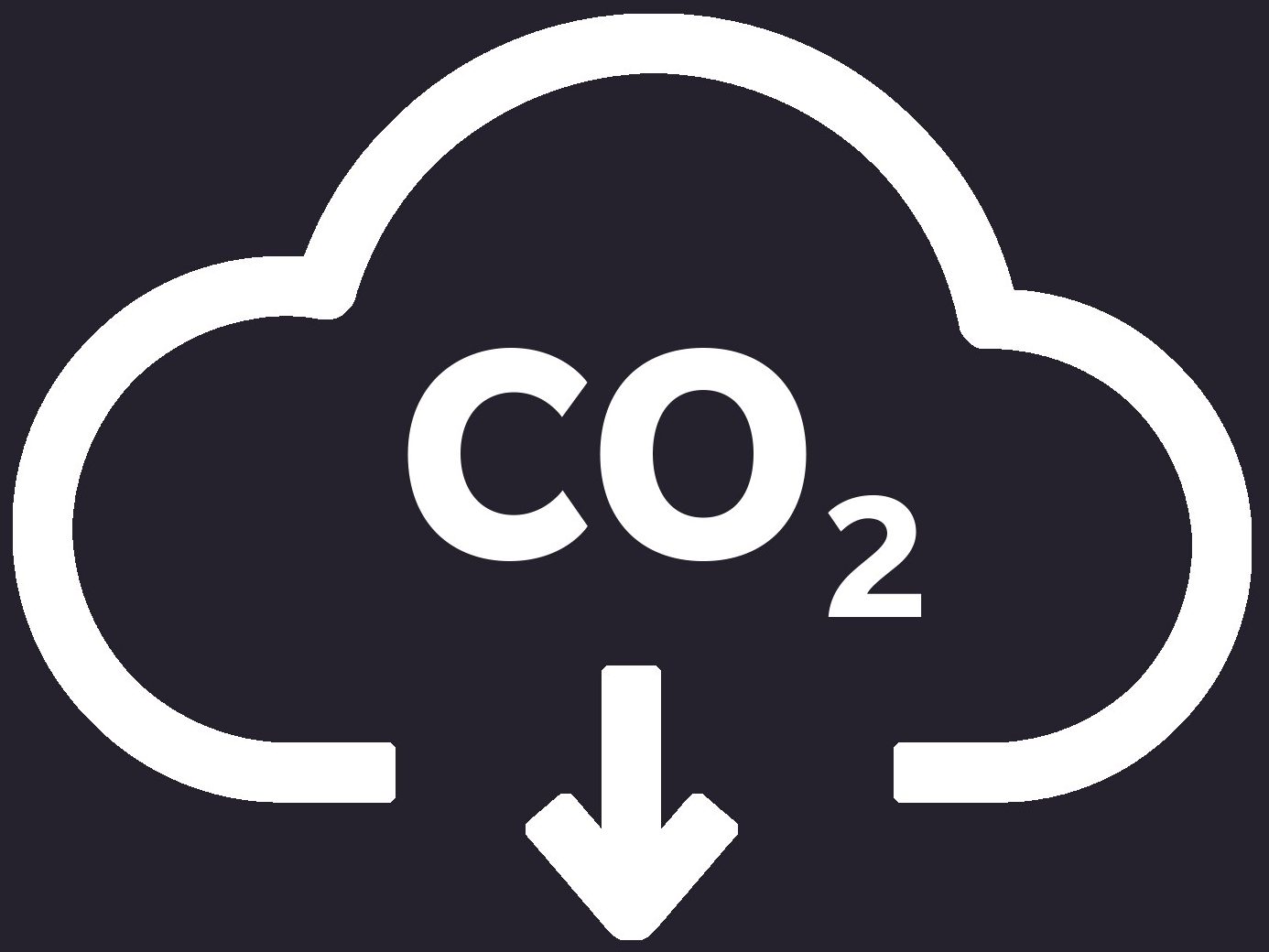
Decarbonization and Energy Mix:
Target and performance
wienberger’s long-term goal is to implement the European Green Deal: By 2050 at the latest, we want to be climate neutral. To this end, we are pursuing a clear strategy set out in our Sustainability Program. We are committed to enhancing energy efficiency in production and transport. In the interest of our customers, we have developed an innovative and sustainable portfolio and are employing new, future-oriented technologies.
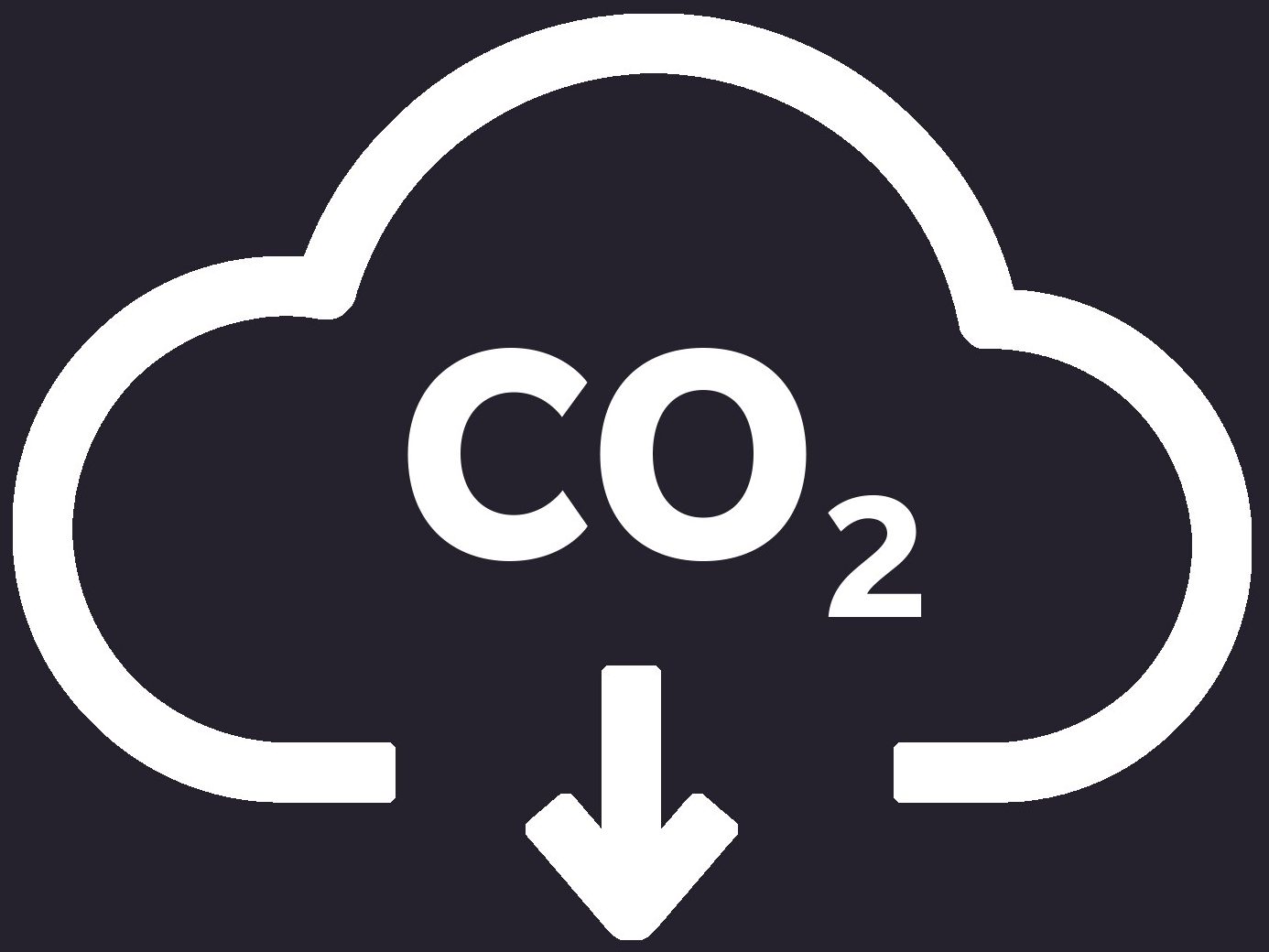
Reduction in scope 1 & 2 CO2 emissions (2020 - 2026)
Reduction in scope 3 CO2 emissions (2022 - 2026)
Success Factors
Last year, we successfully invested in new production technologies and implemented technical optimization projects, enhancing the efficiency and advancement of our production processes. We also optimized our plant network and decarbonized raw material recipes. Additionally, we increased the share of renewable energy by utilizing more green electricity and biogas.
As part of our goal to reduce Scope 3 emissions by 10%, we are optimizing transportation by improving load utilization and integrating low-emission vehicles into our supply chain. We also optimized the cement consumption in concrete blocks and increased the amount of recycled plastics, which have a lower footprint than virgin material.
Best-Practice Examples
We have made significant progress on the path to decarbonization, and here are some exemplary best practices we've implemented to reduce Scope 1 & 2 CO2 emissions:
- Austria, Romania, and Belgium: New production technologies
In the heart of Uttendorf, Austria, wienerberger took a bold step toward sustainability with the Green Bricks project, introducing the world’s first industrial-scale electric kiln powered entirely by green electricity.
New production technologies were implemented in Berca, Romania and Kortemark, Belgium, further enhancing sustainability in manufacturing.
- Netherlands, France, the UK and Austria: Heat pump technology
The transition to green fuels through heat pump technology in Wolfswaard, Netherlands; Segala, France; Sandtoft, United Kingdom; and Uttendorf, Austria, further reduced emissions.
- Hungary: Automation of the process
In Csorna, Hungary, we advanced automation and optimized the drying process, boosting production and energy efficiency.
Adjustments in firing and load curves, product range consolidation, and improved perforation patterns all contributed to energy savings and added customer value. Additionally, Poland's Eco line and Hungary’s Neo line introduced lower-carbon products.
By expanding the production of ECO bricks and brick slips, wienerberger reaffirmed its commitment to a greener future—proving that tradition and innovation can build a more sustainable world.
Scope 3 emission reduction
wienerberger is committed to reducing Scope 3 emissions and optimizing transport efficiency. Across different countries, we implemented sustainable solutions such as:
- Bulgaria and Romania: Concrete products with lower CO2
By adopting cement with a lower clinker content and reducing cement in the recipes, we achieved a significant reduction in CO₂ emissions in Elin Pelin, Bulgaria, and Teiuș, Nadab, Romania. - Bulgaria: Increased use of recycled plastics
We have increased the use of recycled materials, surpassing our internal target for recycled plastics, and nearly reached 300 kg per ton of non-pressure products.
Challenges and Lessons Learned
In a shifting market, we faced several challenges, particularly in the new construction sector, leading to lower plant utilization. By optimizing our plant network and adjusting shift models, we ensured efficient production. Rising costs and limited availability of green energy further impacted operations, along with the expense of bio-based additives. Connecting production facilities to green energy remains challenging. Increased subsidies and streamlined regulatory processes are essential.
Additionally, integrating new technologies comes with a learning curve while heavy-duty e-truck infrastructure is still developing.
Future Commitment
wienerberger is committed to the European Union’s long-term goal of climate neutrality by 2050. To this end, we have established a comprehensive decarbonization roadmap, which we describe in our transition plan and aligns with the Paris Agreement’s 1.5°C target.