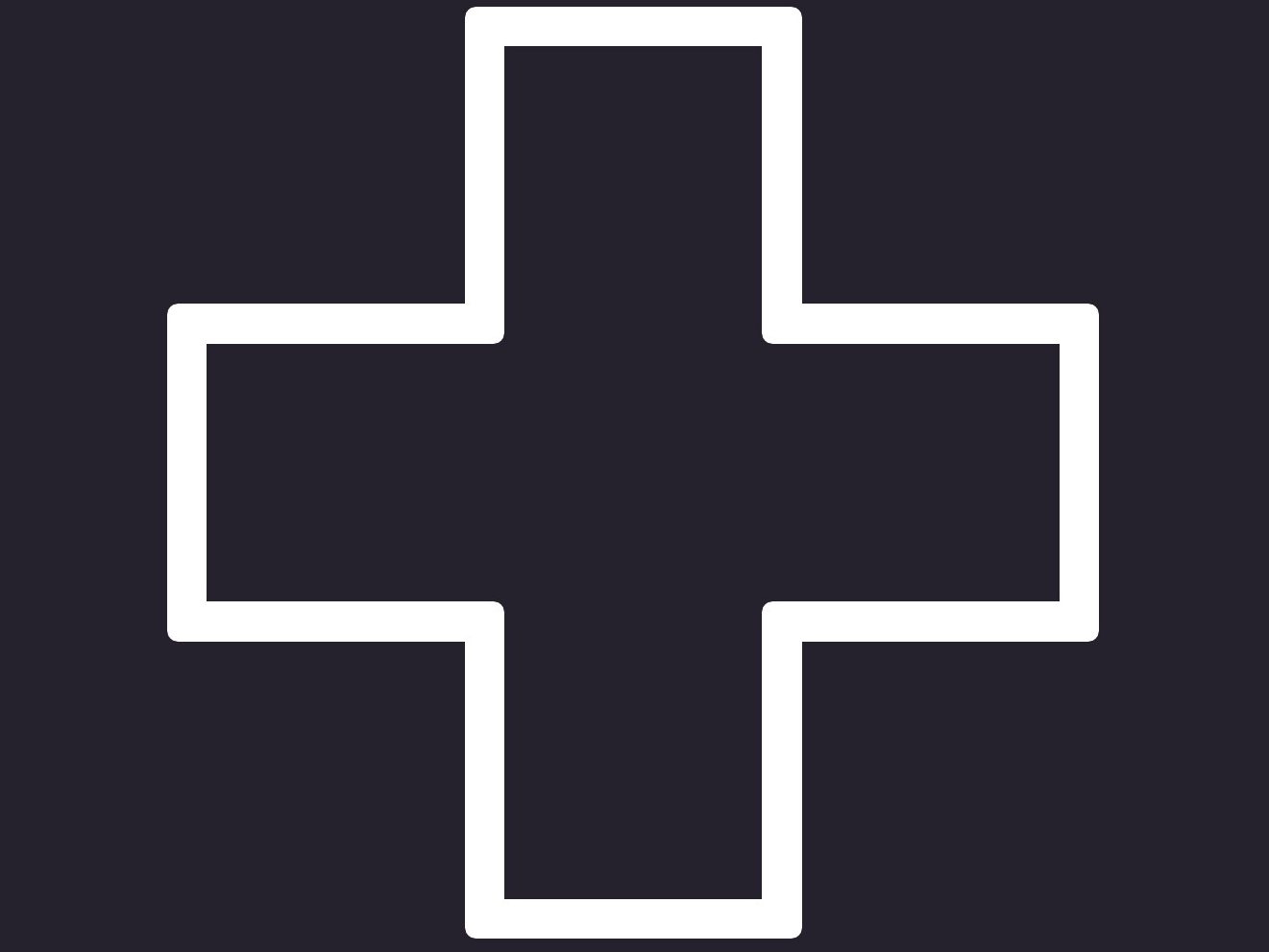
Heath & Safety:
Target and performance
As a social goal within the Sustainability Program 2023-2026, wienerberger continues its focus on personal health and safety, further striving towards the principle of zero harm. This emphasis will be supported by a stronger involvement of management in meetings on safety issues, aiming at 20,000 visible leadership hours.
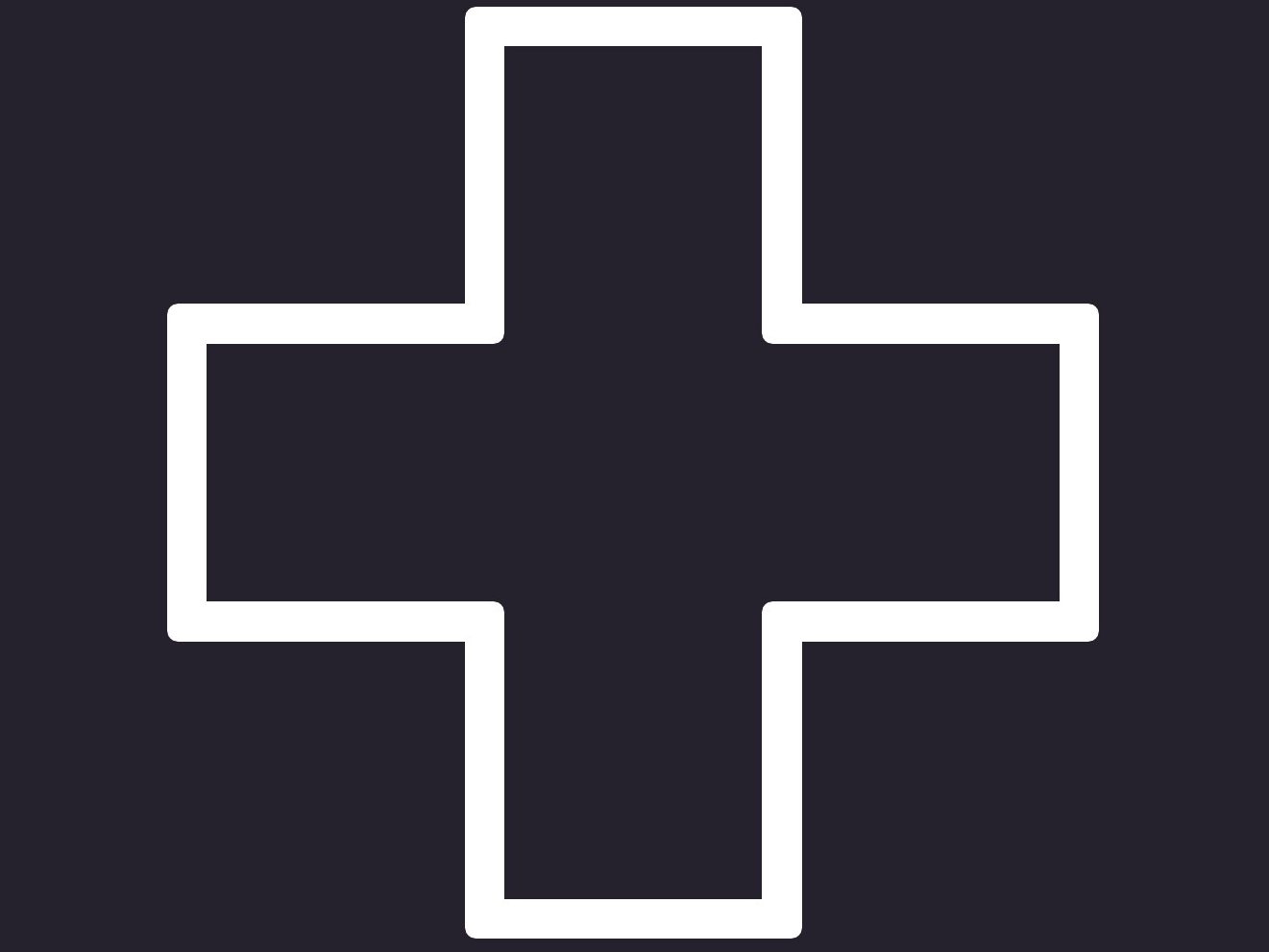
We define a Visible Management Leadership (VML) session as a planned interaction between a member of the local management team and workers at the location where they perform their jobs. The dialogue is about creating awareness of possible risks and how to mitigate these risks.
Success Factors
Visible Management Leadership (VML) is the method wienerberger uses to demonstrate 'Safety Leadership.' Its primary purpose is to enable management teams to show our business commitment to 'Zero Harm' by actively engaging with our workforce on the shop floor.
Local leadership is specifically trained for the VML task to ensure an excellent understanding of how to perform VMLs effectively. We employ various training methods for VML trainers tailored to the distinctive needs of each production plant.
Intercompany best practice sharing has significantly contributed to improving VML implementation.
The original aim was to spend, on average, at least one hour per workforce member on VML. Due to the efforts of our colleagues in 2024, more than double the target number of VML hours were achieved.
Best-Practice Examples
All wienerberger production locations have embraced the VML concept, with some examples we would like to highlight:
- France: Personalized Feedback
The wienerberger country organization in France took an extra step by incorporating coaching and feedback for VML participants into their local Health & Safety program.
- The Netherlands: H&S community
We do our best to facilitate learning across plants through a dedicated H&S community in the Netherlands. Each production site has a designated H&S representative who serves as a local ambassador and advocates for safety initiatives. These representatives meet several times a year to exchange best practices, share experiences, and continuously improve VML’s safety standards.
Challenges and Lessons Learned
The challenge is to change the general mindset of the workforce, ensuring we never sacrifice safety for output and other production metrics. This mentality is what the overarching KPI embodies within Health & Safety, commonly known as P.A.T.H.S. – Positive Attitude Towards Health & Safety.
In 2024, we contributed many VML hours, exceeding our target, as Health & Safety remains our top priority. Our challenge is to maintain our high Health & Safety standards and the number of VML hours in the coming years.
VML remains our most powerful tool for fostering a strong, shared safety culture.
Future Commitment
In the coming years, we will prioritize enhancing the quality of VML hours and optimizing the use of insights gained from them. This dedication will further strengthen their impact on behavioral change.