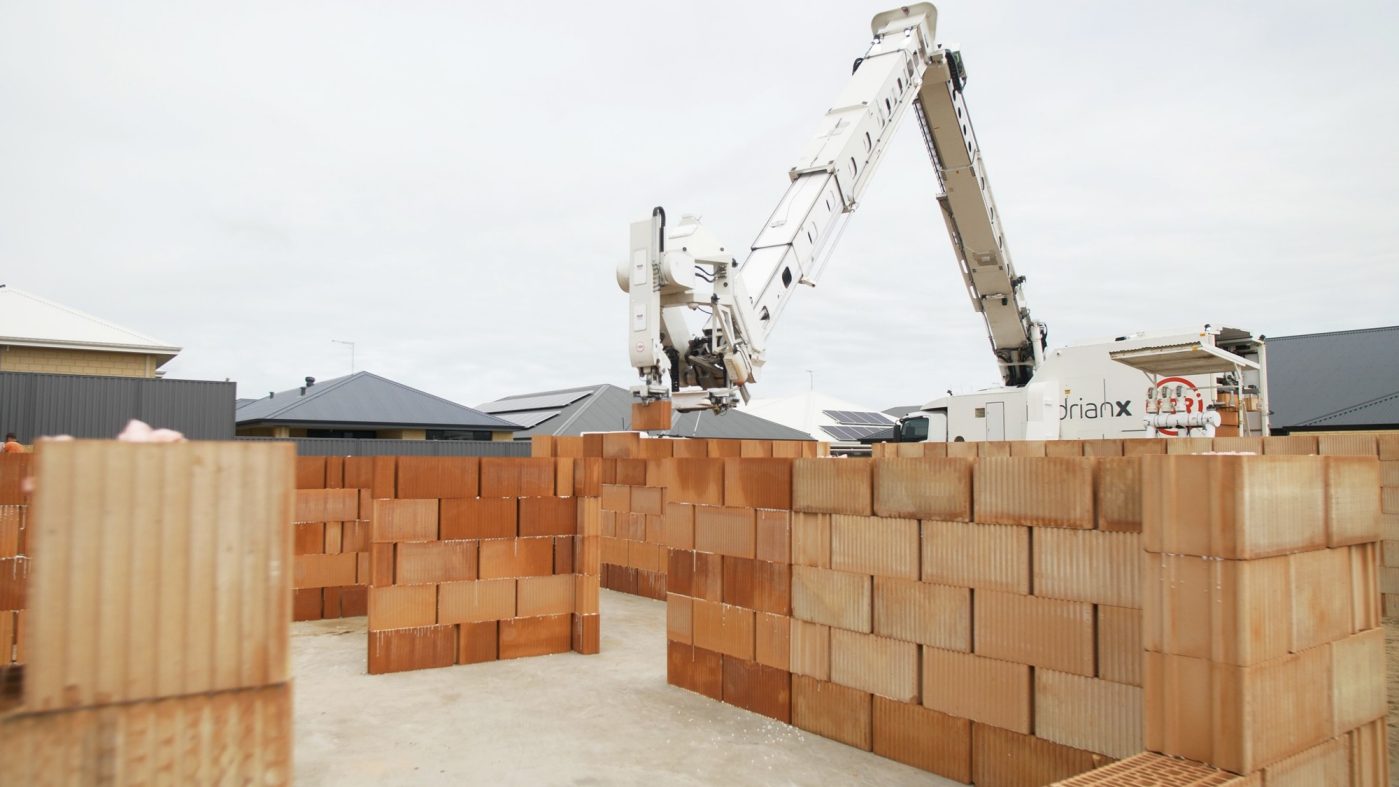
Industry 4.0: wienerberger in Touch with the Future
What opportunities are created by Industry 4.0? wienerberger projects in the area of digital twins, 3D printing, and construction robots provide the answer.
Industry 4.0: wienerberger in Touch with the Future
What opportunities are created by Industry 4.0? wienerberger projects in the area of digital twins, 3D printing, and construction robots provide the answer.
wienerberger is driving automation and digitalization in the construction industry with pioneering applications and system solutions. Industry 4.0 applications can optimize production and increase safety. They can also simplify processes on the construction site, saving both energy and raw materials. Four examples from the world of wienerberger show how.
Industry 4.0 refers to the fourth industrial revolution. Production is optimized by harnessing modern information and communication technology. Intelligent and digitally networked systems enable self-organizing production in which people, machines, plants and products communicate and cooperate directly with each other.
The digital twin is one of the fastest-growing Industry 4.0 applications. As virtual replicas of real-world objects, systems or processes - for example, production plants - digital twins help optimize productivity and efficiency by collecting real-time data from the physical environment and using it in virtual models.
The wienerberger subsidiary Pipelife launched its first digital twin at the Haparanda plant in Finland in 2020. Since then, digital twins have been set up at ten production plants on more than 200 production lines. The operating data collected in the cloud provides valuable information. “The data we obtain with digital twins gives us a much deeper understanding of our production processes. We now waste less material and have more predictable delivery times while having the same high quality our customers expect from us” explains Filipp Pühringer, Pipelife’s expert in Industry 4.0.
Digital twin: Pipelife reproduces the production of plastic pipes in digital form.
Other advantages of using digital twins are increased product traceability and improved reliability thanks to the detection of downtime as well as digitalized production planning, scheduling and monitoring. These steps are crucial when it comes to accelerating production speed and reducing order-to-delivery time. In addition, digital twins offer data transparency for measuring, reporting and assessing the environmental footprint. The technology can thus also contribute to further reducing CO2 emissions.
Pipelife expects to have completed the rollout of digital twin technology to all its plants by the end of 2024. But that is just the beginning: the real-time information that is collected can be used to make forecasts and for ongoing development. “For example, in the future, we are likely to have artificial intelligence trained to propose which production parameters must be adjusted for optimal performance even before the process starts. So, instead of being reactive, we will be able to act proactively. That’s what Industry 4.0 is all about,” says Pühringer.
“Digital twin technology has given us a deeper understanding of our production processes. We now waste less material and have more predictable delivery times while having the same high quality.”
3D printing is another gamechanger in industrial production. This technology is especially helpful when it comes to technically complex requests that are time-consuming to produce manually. In 2020 Pipelife became the first manufacturer to use automated 3D printing to produce manhole and inspection chamber flow profiles. Instead of manually cutting and welding connections for non-standard profiles, specially developed software creates a design with optimized hydraulic properties, and a high-precision 3D printing machine ensures its 1:1 implementation. Due to the increased production speed and the ability to run the printer 24/7, Pipelife now handles more non-standard orders in a shorter time.
Furthermore, 3D printing has opened up new technical possibilities in flow profile design. Pipelife’s software offers more than 400 quadrillion customization options, and the independent test laboratory Deltares has confirmed the excellent hydraulics of 3D-printed flow profiles. Besides optimizing production schedules in the plants, 3D printing has also increased on-the-job safety. The printer produces complete, ready-to-use profiles, eliminating the need for hazardous tasks like manual cutting and welding.
Since introducing automated 3D printing 2.5 years ago, Pipelife has been continuously working on further advancements of the technology. As an example, in 2022 all 3D printers were equipped with conveyor belts, allowing continuous production without human intervention. “We have applied an automatic release system. This means we now continue production during weekends and after 5 pm when our specialists go home,” says Ton Schoenmaker, R&D Project Manager at Pipelife. The group-wide rollout of the new technology continues, and additional 3D printing machines are to join the lineup in the future.
“We have applied an automatic release system. This means we now continue production during weekends and after 5 pm when our specialists go home.”
wienerberger uses 3D printing for the Semmelrock product brand to design and develop new products in-house or to perform function and design checks before a product is launched on the market. “3D printing has simplified our development process and internal communication with other departments and countries. Three-dimensional prototypes make it much easier to coordinate design, product features and functions with customers, even once a product is ready for the market,” explains Gerhard Panzenböck from Strategic Product Development. Then there is the safety check: if the 3D model shows that a product still needs some optimization, this can be done more cheaply than if a production mold has already been made.
Support for communication with customers: 3D-prints help explain Semmelrock solutions and their functions in a way that is easy to understand.
Semmelrock increasingly uses 3D printing to support communication with customers. One example: with the help of 3D prints of scaled-down pavers, architects can be shown features such as systems in the joint for interlocking the slabs. “The advantage is that we can explain a technology or a product to our customers quickly and in way that is very easy to understand,” says Gerhard Panzenböck.
In future, Semmelrock could also use 3D printing in other areas, such as the production of outdoor furniture made of concrete. The advantage: with the help of 3D printing, virtually any geometry can be fabricated from a single cast. This method therefore has valuable potential wherever conventional concrete formwork reaches its limits.
“3D printing has simplified our development process and internal communication with other departments and countries. Three-dimensional prototypes make it much easier to coordinate design, product features and functions with customers even after the product is ready for the market.”
Automation is a crucial element of wienerberger’s response to the challenges facing the construction industry - from the shortage of skilled workers to efficient production. This year a masonry robot belonging to the Australian robotics company Fastbrick Robotics (FBR) became the first to build a complete clay-block house for wienerberger. The two companies had already signed a multi-stage partnership agreement at the end of 2018 to develop an innovative method for laying bricks with robots and to design optimized brick solutions for the masonry robot Hadrian X.
Masonry robot Hadrian X: Brick for brick, a clay-block house was built in Wellard, Australia.
The brick-laying robot built a residential property in Wellard, Australia, with Porotherm bricks produced by wienerberger. The use of the robot accelerates the brick-laying process and thanks to its precision, the bricks can be laid with absolute perfection. Wind and vibrations are measured and balanced in real time. This forward-looking technology will revolutionize residential construction by making it faster, less expensive and more efficient, and guarantee a higher standard of quality. Additionally, the individual bricks are cut in a way that helps save resources and reduces the volume of waste generated.
The automated digital solution is designed for single- and multi-family homes with up to two floors. Depending on the complexity of the project, the fully automated Hadrian X completes the bricklaying process for a house within one to three days. The building just completed followed an outdoor pilot project finished in November 2021. The next step in the Australian pilot project will be the construction of further single- and multi-family homes with wienerberger bricks. The robot could subsequently also be used on the European market.
These examples from wienerberger show the wide-ranging potential of Industry 4.0 for the future of the construction sector. The new possibilities it opens up can simplify decision-making and take some of the pressure off employees. We can’t wait for more innovations!