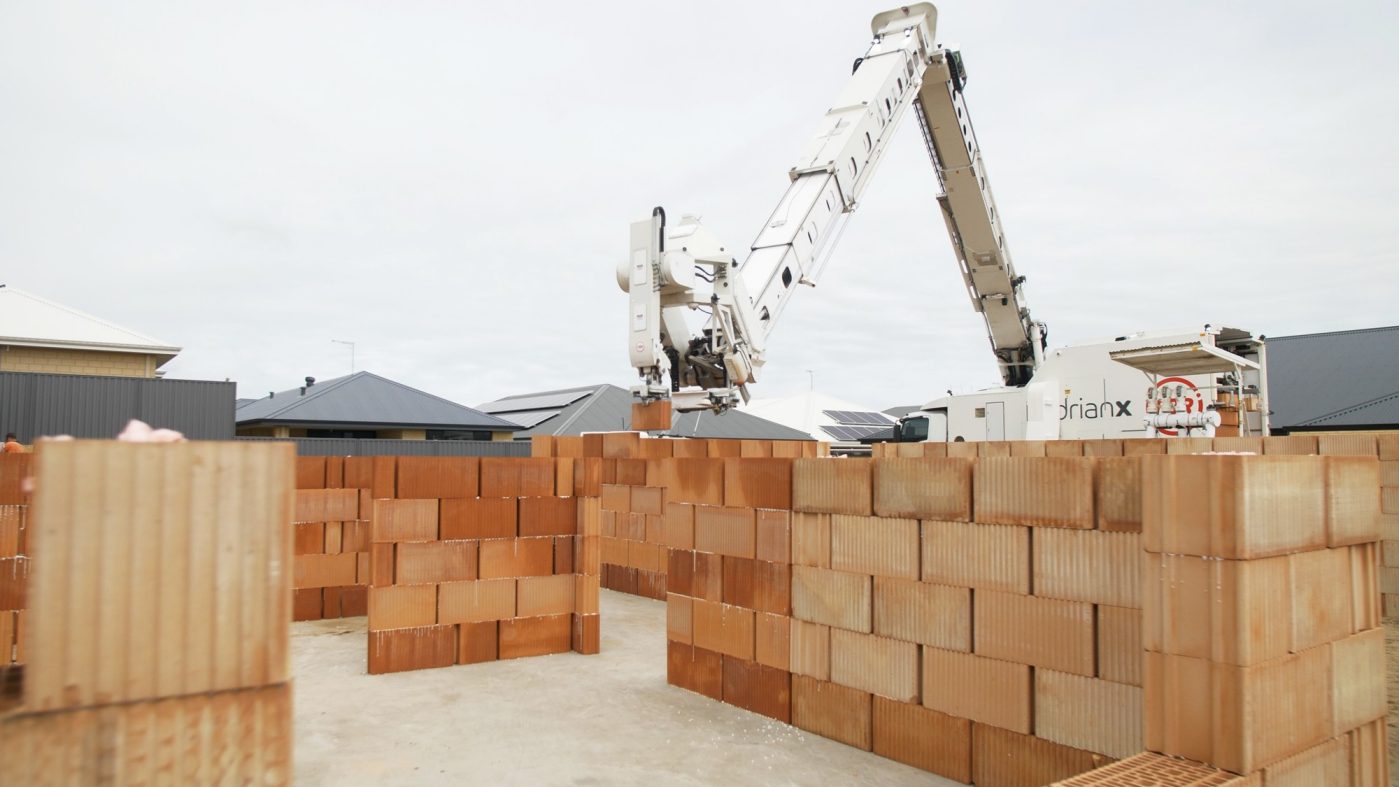
Industrie 4.0: wienerberger am Puls der Zukunft
Welche Möglichkeiten eröffnet die Industrie 4.0? Das zeigen Projekte von wienerberger zu digitalen Zwillingen, 3D-Druck und Robotern am Bau.
Industrie 4.0: wienerberger am Puls der Zukunft
Welche Möglichkeiten eröffnet die Industrie 4.0? Das zeigen Projekte von wienerberger zu digitalen Zwillingen, 3D-Druck und Robotern am Bau.
Mit zukunftsweisenden Anwendungen und Lösungen treibt wienerberger die Automatisierung und Digitalisierung in der Bauindustrie voran. Durch Anwendungen der Industrie 4.0 lässt sich die Leistung in der Produktion optimieren und die Sicherheit erhöhen. Prozesse auf der Baustelle werden vereinfacht und Energie und Rohstoffe eingespart. Wie, erfahren Sie anhand von vier Beispielen aus der Welt von wienerberger.
Der Begriff Industrie 4.0 steht für die vierte industrielle Revolution. Mithilfe moderner Informations- und Kommunikationstechnologie wird dabei die Produktion optimiert. Intelligente und digital vernetzte Systeme ermöglichen eine weitestgehend selbstorganisierte Produktion, in der Menschen, Maschinen, Anlagen und Produkte direkt miteinander kommunizieren und kooperieren.
Sogenannte digitale Zwillinge zählen zu den am schnellsten wachsenden Industrie 4.0-Konzepten. Als virtuelle Nachbildungen realer Objekte, Systeme oder Prozesse – beispielsweise von Produktionsanlagen – ermöglichen sie deren Optimierung durch gezielte Datenerfassung sowie Bildung geeigneter Modelle. Das bringt bessere Leistung und mehr Effizienz.
Die wienerberger Tochter Pipelife führte 2020 den ersten digitalen Zwilling im Werk Haparanda in Finnland ein, seither folgten zehn Produktionsstätten an mehr als 200 Produktionslinien. Die so gesammelten Betriebsdaten in der Cloud liefern wertvolle Informationen. „Durch die digitalen Zwillinge hat sich unser Verständnis für die Produktionsprozesse vertieft. Wir reduzieren Materialverschwendung und haben besser vorhersehbare Lieferzeiten bei gleichbleibend hoher Qualität", erklärt Filipp Pühringer, Experte für Industrie 4.0 bei Pipelife.
Digitaler Zwilling: Pipelife bildet die Produktion von Kunststoffrohren in digitaler Form ab.
Weitere Vorteile durch den Einsatz digitaler Zwillinge sind die bessere Rückverfolgbarkeit der Produkte, mehr Sicherheit durch Detektion von Stillständen sowie eine digitalisierte Produktionsplanung, Terminierung und Überwachung. Dadurch lässt sich die Produktionsgeschwindigkeit erhöhen und die Zeit zwischen Bestellung und Auslieferung weiter verkürzen. Darüber hinaus sind nun transparente Daten für die Messung, Berichterstattung und Bewertung des ökologischen Fußabdrucks verfügbar. Die Technologie kann damit auch zu einer weiteren Reduktion von CO2-Emissionen beitragen.
Bis voraussichtlich Ende 2024 wird der digitale Zwilling in allen Pipelife Werken eingeführt sein. Das ist erst der Beginn: Mit den erfassten Echtzeitinformationen lassen sich Prognosen erstellen und zur Weiterentwicklung nutzen. „In Zukunft könnten wir zum Beispiel mithilfe künstlicher Intelligenz bestimmen, welche Produktionsparameter für eine optimale Leistung angepasst werden müssen, bevor der Prozess überhaupt beginnt. Statt reaktiv zu sein, werden wir also proaktiv handeln können. Das ist es, worum es bei Industrie 4.0 geht“, so Pühringer.
„Durch die digitalen Zwillinge hat sich unser Verständnis für die Produktionsprozesse vertieft. Wir verlieren nun weniger Material und haben besser vorhersehbare Lieferzeiten bei gleichbleibend hoher Qualität.“
Als Gamechanger erweist sich auch der 3D-Druck in der industriellen Produktion. Diese Technologie ist vor allem bei technisch komplexen Anwendungen hilfreich, deren manuelle Herstellung zeitaufwändig ist. Im Jahr 2020 war Pipelife der weltweit erste Hersteller, der den automatisierten 3D-Druck zur Herstellung von Durchflussprofilen für Schächte und Kontrollschächte einsetzte. Anstelle des manuellen Schneidens und Schweißens von Verbindungen für komplexere Profile erstellt eine speziell entwickelte Software ein Design mit optimierten hydraulischen Eigenschaften. Eine hochpräzise 3D-Druckmaschine sorgt für die 1:1-Umsetzung. Dank der höheren Produktionsgeschwindigkeit und der Möglichkeit, den Drucker rund um die Uhr laufen zu lassen, kann Pipelife mehr solcher Aufträge in kürzerer Zeit bearbeiten.
Zudem hat der 3D-Druck neue technische Potenziale bei der Konstruktion eröffnet. Die Software von Pipelife bietet mehr als 400 Billiarden Anpassungsmöglichkeiten und das unabhängige Testlabor Deltares hat die hervorragende Hydraulik der so gedruckten Durchflussprofile bestätigt. Neben den Produktionsabläufen hat der 3D-Druck außerdem die Arbeitssicherheit in den Werken verbessert. Der Drucker produziert komplette, gebrauchsfertige Profile, wodurch das händische Schneiden und Schweißen als Gefahrenquelle ausscheidet.
Seit der Einführung des automatisierten 3D-Drucks vor zweieinhalb Jahren hat Pipelife die Technologie kontinuierlich weiterentwickelt. So wurden 2022 alle 3D-Drucker mit Förderbändern ausgestattet, was eine laufende Produktion ohne menschlichen Eingriff ermöglicht. „Wir haben ein automatisches Freigabesystem eingesetzt. Das bedeutet, dass wir jetzt auch am Wochenende und nach 17 Uhr, wenn unsere Fachkräfte nach Hause gehen, weiter produzieren können“, sagt Ton Schoenmaker, F&E-Projektmanager bei Pipelife. Die gruppenweite Einführung der neuen Technologie wird fortgesetzt: In Zukunft sollen weitere 3D-Druckmaschinen ihre Arbeit aufnehmen.
„Wir haben ein automatisches Freigabesystem eingesetzt. Das bedeutet, dass wir jetzt auch am Wochenende und nach 17 Uhr, wenn unsere Fachkräfte nach Hause gehen, weiter produzieren können.“
wienerberger setzt bei der Produktmarke Semmelrock 3D-Druck intern beim Design und der Entwicklung neuer Produkte oder für den Funktionalitäts- und Designcheck vor der Marktreife ein. „Der 3D-Druck hat unseren Entwicklungsprozess und die interne Kommunikation mit anderen Abteilungen und Ländern erleichtert. Anhand dreidimensionaler Prototypen lassen sich Design, Produkteigenschaften und -funktionen auch nach der Marktreife mit Kunden wesentlich einfacher abstimmen“, erklärt Gerhard Panzenböck von der strategischen Produktentwicklung. Dazu kommt der Sicherheitscheck: Ergibt sich anhand des 3D-Modells noch Optimierungsbedarf, so lässt sich dies kostengünstiger umsetzen, als wenn bereits eine Produktionsform erstellt wurde.
Unterstützung im Kundengespräch: 3D-Drucke helfen, Lösungen von Semmelrock und ihre Funktionen anschaulich zu erklären.
Semmelrock verwendet den 3D-Druck auch vermehrt als Unterstützung bei der Kommunikation mit Kundinnen und Kunden. Ein Beispiel: Mithilfe von 3D-Druck können Architektinnen und Architekten anhand maßstäblich verkleinerter Pflastersteine bestimmte Funktionalitäten anschaulich gezeigt werden – etwa ein Interlocking-System in der Fuge zur Verzahnung der Platten. „Der Vorteil ist, dass wir unseren Kundinnen und Kunden so eine Technologie oder ein Produkt auf sehr einfache Weise rasch erklären können“, so Gerhard Panzenböck.
In Zukunft könnte der 3D-Druck bei Semmelrock in weiteren Bereichen zum Einsatz kommen. Ein Beispiel sind Outdoor-Möbel aus Beton. Der Vorteil: Mithilfe von 3D-Druck lässt sich so gut wie jeder geometrische Körper aus einem Guss schaffen. Daher könnte dieses Verfahren überall dort Potenzial bieten, wo die klassische Betonschalung an ihre Grenzen stößt.
„Der 3D-Druck hat unseren Entwicklungsprozess und die interne Kommunikation mit anderen Abteilungen und Ländern erleichtert. Anhand dreidimensionaler Prototypen lassen sich Design, Produkteigenschaften und -funktionen auch nach der Marktreife mit Kunden wesentlich einfacher abstimmen.“
Um den aktuellen Herausforderungen in der Bauindustrie (von Fachkräftemangel bis zu effizienter Fertigung) zu begegnen, setzt wienerberger unter anderem auf Automatisierung. Heuer baute der Bauroboter des australischen Robotikunternehmens Fastbrick Robotics (FBR) erstmals ein komplettes Hintermauerziegel-Haus für wienerberger. Bereits Ende 2018 wurde ein mehrstufiges Partnerschaftsabkommen mit FBR unterzeichnet. Das Ziel: eine innovative Methode für das Verlegen von Ziegeln mit Robotern zu entwickeln und für den Bauroboter Hadrian X optimierte Ziegellösungen zu schaffen.
Bauroboter Hadrian X: Schritt für Schritt entstand im australischen Wellard ein Haus aus Hintermauerziegeln.
Der auf Ziegelmauerwerk spezialisierte Bauroboter hat nun im australischen Wellard mit Porotherm-Ziegeln von wienerberger ein Wohnhaus errichtet. Der Einsatz des Roboters beschleunigt die Verarbeitung. Durch seine Präzision können Ziegel millimetergenau verarbeitet werden. Wind und Erschütterungen werden in Echtzeit gemessen und austariert. Mit dieser zukunftsweisenden Technologie lässt sich Wohnraum künftig schneller, günstiger und effizienter in einem hohen Qualitätsstandard realisieren. Zusätzlich werden die einzelnen Ziegel ressourcenschonend geschnitten, was den dabei entstehenden Abfall verringert.
Die automatisierte und digitale Lösung ist für Einfamilienhäuser und Mehrfamilienhäuser mit bis zu zwei Stockwerken konzipiert. Je nach Schwierigkeitsgrad schafft der vollautomatisierte Hadrian X die Fertigstellung eines Hauses in ein bis drei Tagen. Der aktuelle Bau folgte auf ein im November 2021 abgeschlossenes Pilotprojekt im Freien. Im Rahmen des australischen Pilotprojekts werden im nächsten Schritt weitere Einfamilien- und Mehrfamilienhäuser mit wienerberger Ziegeln gebaut. In der Folge könnte der Roboter auch am europäischen Markt Einsatz finden.
Die Beispiele von wienerberger zeigen: Die Industrie 4.0 bietet vielfältiges Potenzial für die Zukunft der Bauindustrie. Ihre neuen Möglichkeiten können Entscheidungen erleichtern und Mitarbeitende in ihrer Arbeit entlasten. Wir sind gespannt auf weitere Innovationen!